Get reliable results with expert plastic extrusion techniques
Get reliable results with expert plastic extrusion techniques
Blog Article
Understanding the Basics and Applications of Plastic Extrusion in Modern Production
In the realm of modern-day production, the strategy of plastic extrusion plays an instrumental duty - plastic extrusion. This elaborate process, entailing the melting and shaping of plastic with specialized dies, is leveraged throughout various industries for the production of diverse items. From vehicle components to consumer items packaging, the applications are substantial, and the possibility for sustainability is equally excellent. Untangling the basics of this process discloses the real convenience and potential of plastic extrusion.
The Basics of Plastic Extrusion Process
While it might show up complex, the fundamentals of the plastic extrusion procedure are based upon fairly straightforward principles. It is a production process in which plastic is thawed and afterwards shaped into a continuous profile through a die. The raw plastic product, often in the form of pellets, is fed into an extruder. Inside the extruder, the plastic undergoes warm and stress, causing it to melt. The molten plastic is after that compelled with a designed opening, called a die, to form a long, continual product. The extruded item is cooled and after that reduced to the wanted size. The plastic extrusion procedure is extensively used in various sectors as a result of its effectiveness, cost-effectiveness, and versatility.
Different Sorts Of Plastic Extrusion Strategies
Structure upon the basic understanding of the plastic extrusion procedure, it is necessary to discover the various methods involved in this production technique. The two primary techniques are profile extrusion and sheet extrusion. In account extrusion, plastic is thawed and formed into a constant account, frequently utilized to develop pipes, poles, rails, and home window frameworks. In comparison, sheet extrusion produces big, level sheets of plastic, which are usually additional refined right into products such as food product packaging, shower drapes, and automobile components. Each technique calls for specialized machinery and accurate control over temperature and pressure to guarantee the plastic preserves its form throughout cooling. Understanding these techniques is crucial to utilizing plastic extrusion effectively in modern-day production.
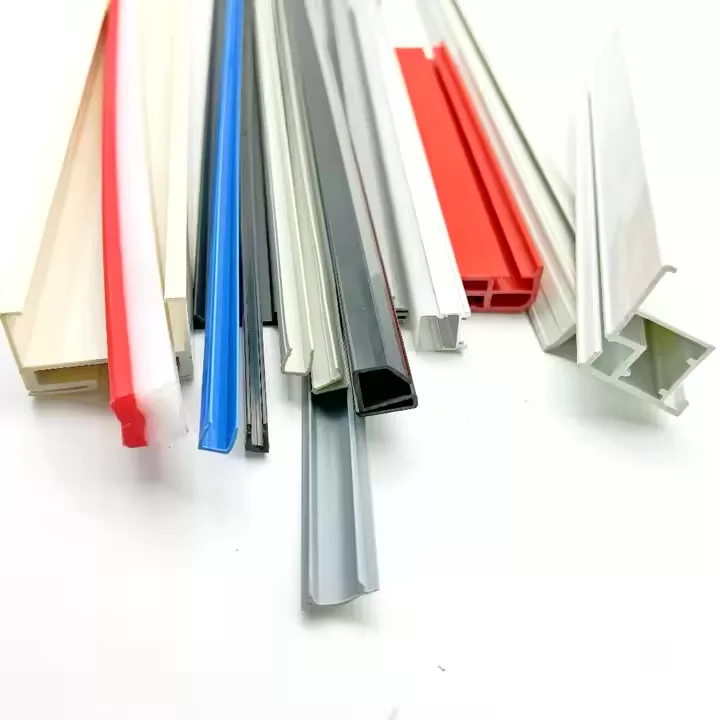
The Duty of Plastic Extrusion in the Automotive Industry
A frustrating majority of parts in modern vehicles are products of the plastic extrusion procedure. This procedure has actually changed the automotive market, changing it right into an extra reliable, economical, and versatile manufacturing industry. Plastic extrusion is mainly used in the manufacturing of various automobile elements such as bumpers, grills, door panels, and dashboard trim. The process supplies an attire, consistent result, allowing suppliers to generate high-volume get rid of wonderful precision and very little waste. The lightness of the extruded plastic components contributes to the overall reduction in vehicle weight, boosting gas effectiveness. The durability and resistance of these parts to warm, cool, and influence enhance the longevity of vehicles. Thus, plastic extrusion plays an essential role in automotive manufacturing.
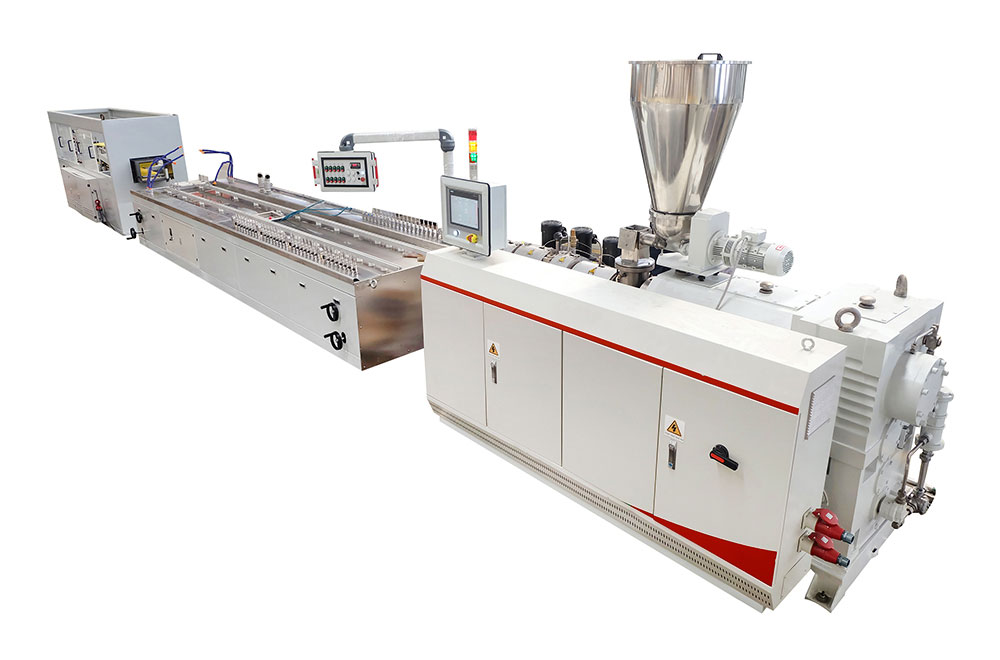
Applications of Plastic Extrusion in Customer Goods Production
Past its considerable impact on the automobile sector, plastic extrusion confirms similarly efficient in the world of customer items manufacturing. The versatility of plastic extrusion permits makers to design and produce complex forms and sizes with high accuracy and efficiency. The adaptability, adaptability, and cost-effectiveness of plastic extrusion make it a preferred choice for lots of consumer products manufacturers, contributing dramatically to the sector's growth and innovation.
Ecological Impact and Sustainability in Plastic Extrusion
The pervasive use plastic extrusion in manufacturing invites scrutiny of its environmental implications. As a procedure that regularly uses non-biodegradable products, the check this environmental impact can be substantial. Energy usage, waste production, and carbon exhausts are all worries. Market innovations are boosting sustainability. Reliable equipment minimizes power click usage, while waste management systems recycle scrap plastic, reducing raw material needs. In addition, the advancement of eco-friendly plastics supplies a more ecologically friendly option. In spite of these improvements, even more innovation is needed to reduce the ecological impact of plastic extrusion. As society leans towards sustainability, suppliers need to adapt to remain feasible, emphasizing the relevance of continuous research study and innovation in this field.
Verdict
In conclusion, plastic extrusion plays an essential duty in modern manufacturing, particularly in the vehicle and consumer goods fields. Comprehending the fundamentals of this process is crucial to maximizing its applications and advantages.
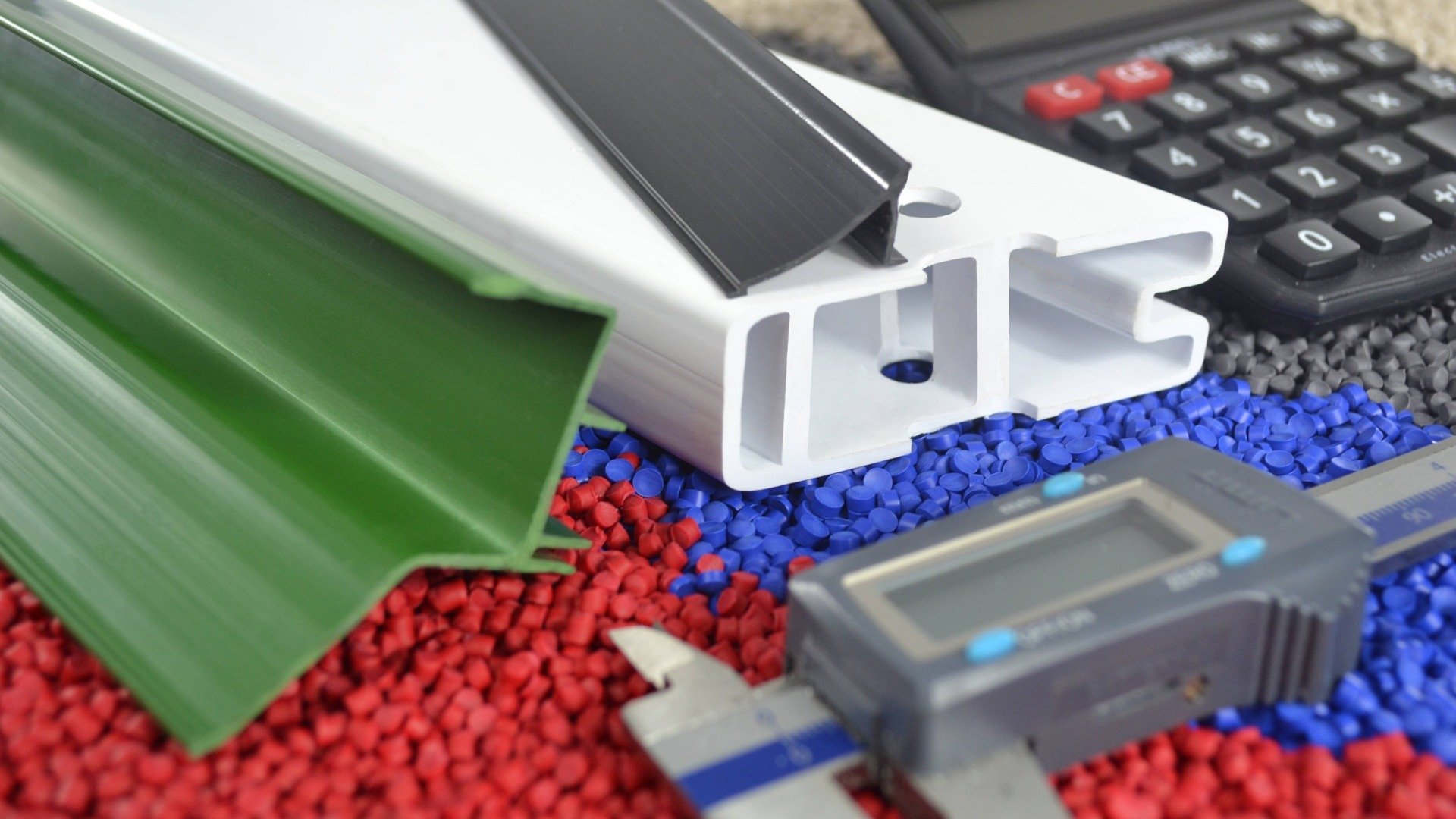
The plastic extrusion process is thoroughly utilized in numerous markets due to its versatility, cost-effectiveness, and performance.
Building upon the basic understanding of the plastic extrusion process, it is necessary to discover the various methods entailed in this production approach. plastic extrusion. In contrast, sheet extrusion develops huge, level sheets of plastic, which are commonly additional processed into items such as food packaging, shower curtains, and vehicle components.A frustrating majority of components in modern automobiles are items of the plastic extrusion process
Report this page